- FMA
- The Fabricator
- FABTECH
- Canadian Metalworking
Categories
- Additive Manufacturing
- Aluminum Welding
- Arc Welding
- Assembly and Joining
- Automation and Robotics
- Bending and Forming
- Consumables
- Cutting and Weld Prep
- Electric Vehicles
- En Español
- Finishing
- Hydroforming
- Laser Cutting
- Laser Welding
- Machining
- Manufacturing Software
- Materials Handling
- Metals/Materials
- Oxyfuel Cutting
- Plasma Cutting
- Power Tools
- Punching and Other Holemaking
- Roll Forming
- Safety
- Sawing
- Shearing
- Shop Management
- Testing and Measuring
- Tube and Pipe Fabrication
- Tube and Pipe Production
- Waterjet Cutting
Industry Directory
Webcasts
Podcasts
FAB 40
Advertise
Subscribe
Account Login
Search
Welding tool steel
Many manufacturers are suspicious of welding repairs on tooling, but if done right, they can last a long time
- By Miguel Ernesto Mendez Obregon
- January 17, 2019
- Article
- Arc Welding
Editor’s Note: This article originally appeared in the Winter 2018 edition of The FABRICATOR en Español.
A lot of questions surround the topic of tool steel welding. Welders often don’t agree on how it is supposed to be done, and there is misinformation about the proper application of the process and how to do it successfully. And diemakers disagree on whether it’s right to weld a die to perform an adjustment, or only to repair the die, or if it’s just not a good practice at all. Some believe that a weld won’t last, eventually damaging the die and decreasing the life of the tool.
It is true that a weld won’t last as long as tool steel. And it’s true that if a broken die is repaired with poor welding, part galling can occur, or the die could fall apart during a production run.
But it’s also true that welding can be a handy tool if it is applied properly, and it can last a very long time if you take certain factors into consideration.
Tool steel is designed to be resistant to wear and impact, with a hardness high enough to cut another steel. Those characteristics make tool steel react differently than conventional steel when subjected to welding. Knowing how tool steel reacts to welding can help you ensure good results.
Making Repairs and Adjustments With Welding
Welding can be used to repair a broken die, fill in chipped surfaces, fix damaged sharp edges, and recover worn features, but it should be your last resort. If you have the option to machine and recover the surface or grind a chipped zone and shim back again, don’t weld.
Sometimes during the development of new dies, features need to be developed by trial and error, so it’s not feasible or reasonable to machine several different versions of the same insert with minimal modifications among them. Often after a die is first run, the part will need adjustment during assembly, which means the part designer needs to change the profile. If the change is something like moving a trim edge, you can achieve it with welding and continue fine-tuning until the die produces a good part. Once the part is in its final, correct form, you can measure the trim steel and make a new die.
Part Holding for Welding
In general, gas tungsten arc welding (GTAW) is the best process to use on tool steel based on its amperage and control over feeding and aim. Gas metal arc welding is a better choice for fast filling and joining large pieces.
If welding is the only choice, then you need to analyze the insert to find the best way to hold it during welding. It must be held square during the whole process or a mismatch could occur that creates more problems later.
When analyzing the broken insert, identify the original support area and look for bumps and distortion that could create a fit problem. Try to assemble it to see how all the pieces fit together. If a piece is too small to hold during the welding process, discard it and fill the gap with welding instead.
Once you have identified the original backrest of the insert and have decided that one of the sides can be used to ensure squareness, you might need to machine flat metal pieces to use to hold down the part during welding. Remember, those pieces must be thick enough to withstand the distortion that can occur after welding.
Bevel Width and Depth
After you have identified the flats and the contact or squareness zones, prepare the pieces to be welded by making a bevel in all the zones that have contact with the other pieces. For example, if the pieces that will be welded have a triangular shape, you need to bevel the three sides of the part that have contact with other pieces.
There is no steadfast rule on how wide and deep the bevel must be, because it depends on the specific situation. But remember that you must ensure the weld has enough penetration and that you have enough contact between the pieces to make them fit. In general, if you make the bevel depth about one-third of the total piece thickness, you will achieve proper weld penetration. This depth ensures you have enough land or reference to align the pieces with one another.
The bevel width is important because it helps ensure the weld is applied properly from the root. If you use a minimum angle of 45 degrees, you’ll have enough room to weld at the root, aim properly, and feed without problems. In addition, the final weld seam bead will be better because there is more area to apply enough welding to avoid missing areas between weld seams and causing pores.
Be sure to look for cracks and fractures that can detach from the piece, and grind away any that you find. When using GTAW, always sharpen the tungsten toward the stone and not against it, because that will affect the flow of the gas and therefore the shield.
The Case for Preheating
Preheating is a critical step in welding that often is underestimated. Welders believe if they’re not going to weld a large section, preheating is unnecessary before welding. However, the size of the section isn’t the concern. Regardless of the size of the section being welded, the weld zone is affected by the temperature of the welding. The effect of that heat on the weld zone, and how to handle it in a proper way to ensure the proper result, is the true concern.
Preheating prepares the steel to handle the temperature imparted by the welding process. There is a tremendous difference between a base metal at ambient temperature (72 degrees F) and the heat in the weld puddle (1,800 degrees F).
The temperature around the weld puddle decreases with distance from it, so while some parts of the steel are expanding, others are already contracting. That creates distortion and cracking.
Keep in mind that tool steels are medium- and high-carbon steels, which makes them susceptible to hardness after reaching high temperatures. This means that when the material goes from 72 to 1,800 degrees F in seconds, the steel will become very brittle. Preheating reduces the drastic difference in these temperatures and helps the steel handle the change. But while you want to reduce the difference between temperatures, you don’t want to temper the steel and reduce the hardness. You are repairing the insert, so you want to keep the same hardness as much as possible.
Therefore, a rule of thumb for the length of preheating is to use the same amount of time that you used at the last tempering of the steel, but at 212 degrees F below the tempering temperature. In this way, you can ensure that you bring the material to the right temperature, evenly throughout the whole piece, without tempering the steel.
Make sure that the part is clean before going to the furnace. If any lubricants or oils remain on the part, they can affect the shield created by the inert gas to prevent oxidation. Any impurity left behind to burn during welding can create porosity.
If you don’t have a furnace, you can use an open flame from a torch and measure the temperature with temperature-indicating crayons. You might also be able to identify temperature by the color of the insert, although this is not exact. A good reference is a brown-yellow color.
Welding Rod
The choice of welding rod depends on the type of steel that is going to be welded and its application. For instance, you can’t use the same type of welding rod to repair a sharp cutting edge as you would use to join pieces.
In general, there are two types of rods: soft and hard. Soft rods are designed to have flexibility and low strength. They deflect on impact and will not crack or chip. Soft rods are used to make a base or cushion layer because they create the proper bond between the parts and minimize the brittleness of the union.
When repairing an insert, you create the cushion layer, which is needed to join the pieces, and then continue building up. Depending on the function of the insert, you need to decide how much room to leave to apply the hard rod. And keep in mind that some hard rods don’t react well when you apply several layers. Since hard rods are designed to achieve hardness, they don’t have much flexibility, and when the material is cooling down after welding, it might crack.
Miguel Ernesto Mendez Obregon can be reached at miguel-ernesto@live.com.mx.
About the Author
Miguel Ernesto Mendez Obregon
subscribe now
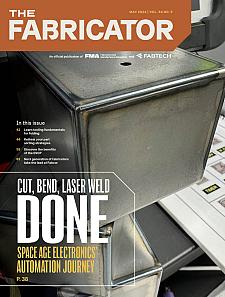
The Fabricator is North America's leading magazine for the metal forming and fabricating industry. The magazine delivers the news, technical articles, and case histories that enable fabricators to do their jobs more efficiently. The Fabricator has served the industry since 1970.
start your free subscription- Stay connected from anywhere
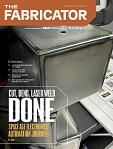
Easily access valuable industry resources now with full access to the digital edition of The Fabricator.
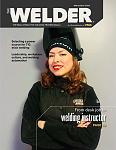
Easily access valuable industry resources now with full access to the digital edition of The Welder.
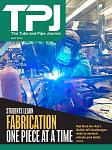
Easily access valuable industry resources now with full access to the digital edition of The Tube and Pipe Journal.
- Podcasting
- Podcast:
- The Fabricator Podcast
- Published:
- 04/16/2024
- Running Time:
- 63:29
In this episode of The Fabricator Podcast, Caleb Chamberlain, co-founder and CEO of OSH Cut, discusses his company’s...
- Industry Events
16th Annual Safety Conference
- April 30 - May 1, 2024
- Elgin,
Pipe and Tube Conference
- May 21 - 22, 2024
- Omaha, NE
World-Class Roll Forming Workshop
- June 5 - 6, 2024
- Louisville, KY
Advanced Laser Application Workshop
- June 25 - 27, 2024
- Novi, MI